C 3.4 SOLID ALUMINUM ELECTROLYTICS (SAL) with MANGANESE DIOXIDE (obsolete capacitor technology)
The SAL are aluminum electrolytic capacitors with anodic oxidized aluminum oxide as dielectric and with the semiconducting solid manganese dioxide as electrolyte. They are made of etched and formed aluminum anodes, which are folded for the dipped pearl types or wound into a roll for the axial style. The solid manganese dioxide electrolyte is formed onto this roll in a pyrolytic process, similar to that for solid tantalum capacitors.
SAL-capacitors were developed and introduced in the market in the 1960s by Philips. Up until December 30, 2015, it was a single source product manufactured by Vishay.
As of December 31, 2015 the SAL are end-of-life and have ceased production. Nevertheless, we still list the technology features here for comparison and overview.
C 3.4.1 Introduction
The electrolyte is a solid one. Thus, life is independent of drying effects and leakage currents and theoretically unlimited. Storage has no impairing effect on the dielectric. The stability is much better than that of wet types. The capacitance tolerance is ±20%. The price is high.… Compared to solid tantalums the price for solid aluminum (Al) electrolytics of the same CV product is between two and three times higher. The solid electrolyte doesn’t penetrate the pores of the highly etched aluminum foil equally well as a wet one. Its conductivity, however, is between one and two orders of magnitude larger than that of the wet electrolyte and its temperature dependence smaller.
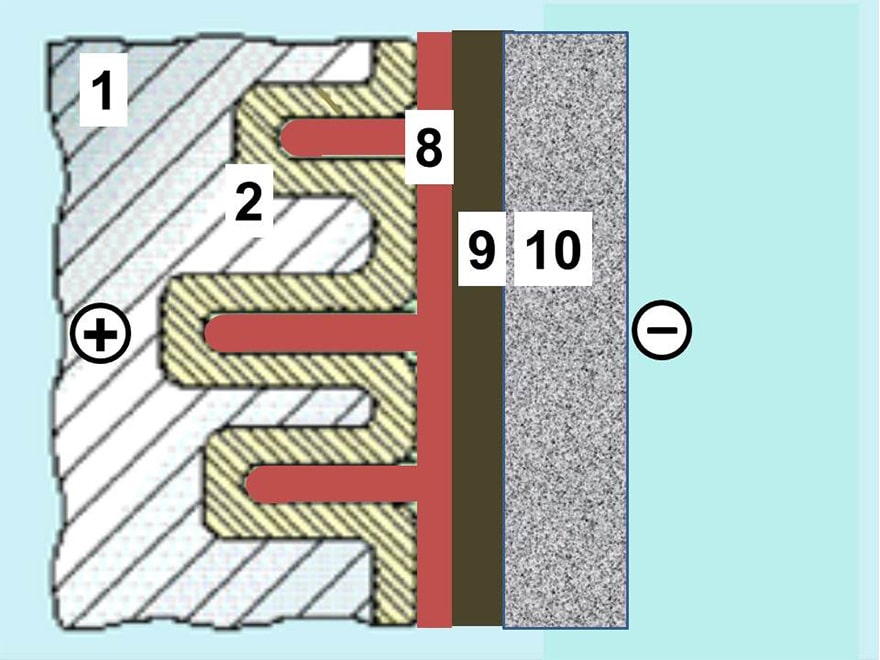
Thus, the solid Al electrolytic is relatively insensitive to the pore effect that in wet Al electrolytics creates a deep network of series and parallel resistances as was shown in Figure C3-13. The capacitor can’t stand any breakdowns. This requires large margins between the forming and rated voltages. The forming rate usually is 2 to 3 times and the rated voltage maximum 40 V DC. Unlike solid tantalums the capacitor is relatively insensitive to pulse loads which, among other things, depends on its higher ESR that reduces the need for an additional circuit impedance.
Nevertheless, just as in solid tantalums, very high pulse currents can initiate a fire. There were two construction styles on the market, the epoxy encapsulated radial types for maximum 175 °C and the axial aluminum can type designed for maximum 200 °C. The radial lead design has a stacked aluminum plate construction which renders a very low ESL (equivalent series inductance). It ranged from 9 to 20 nH. The cylindrical can has a winding of anode and cathode foils plus glass fiber spacers. The reliability of the cylindrical can types is high. Of these there are designs with epoxy fillings intended for extreme acceleration and shock stress.
C 3.4.2 Properties
Capacitance versus temperature
Both the radial and the axial lead types are represented in Figure C3-36.
ESR versus temperature
In comparison with wet aluminum electrolytics (Figure C3-28) ESR of the solid ones have a less pronounced temperature dependence as shown in Figure C3-37.
ESR versus frequency Typical normalized diagrams are shown in Figure C3-38 and 39. The former concerns the radial lead designs with their lower ESL and higher operating frequency range.
Note the lower frequency range of the following axial lead design. The steeper slope of the diagrams in the lower part of the frequency range depends on the oxide losses (Figure C3-39).
The ESR characteristics are poorer than those of solid tantalums, especially at cooler temperatures. In other word the impedance curve levels off and touches the ESR bottom at lower frequencies in solid Al electrolytics of comparable sizes.
Leakage current versus temperature
In Table C3-2 we referred to standards and depicted time to reading to 5 minutes. Figure C3-22 shows a comparison between the time dependence of solid and wet tantalums. In the solid type the curve levels out relatively quick. The same also applies to solid Al electrolytics. Thus, DCL often is measured already after 15 seconds or 1 minute.
C 3.4.3 Reverse voltage
The permissible reverse voltage is stated to be:
- @ ≤ 85°C max 0.3 x VR
- @ 85 → 125°C from max 0.3xVR → max 0.15xVR
C 3.4.4 Failure modes
Epoxy-dipped types with radial leads are sensitive to mechanical forces applied on the leads at mounting. Inappropriate handling results in an increase of the leakage current.
ABC of CLR: Chapter C Capacitors
Solid Aluminum Electrolytics with Manganese Dioxide (obsolete capacitor technology)
EPCI licenced content by:
[1] EPCI European Passive Components Institute experts original articles
[2] CLR Passive Components Handbook by P-O.Fagerholt*
*used under EPCI copyright from CTI Corporation, USA
This page content is licensed under a Creative Commons Attribution-Share Alike 4.0 International License.
see the previous page:
< Page 19 >
see the next page: