Carbon is one of the basic elements that has been used in electronics for a long time. Carbon occurs in various forms (allotropes) such as graphite, diamond, carbon nanotubes or graphene. In particular, carbon nanotubes and graphene are increasingly used in the field of electronic components and sensors. Carbon nanotubes can be modified by organic or inorganic substances and based on this to change their properties. Modified carbon nanotubes are preferably used as sensitive layers in environmental sensors. With the help of these materials, it is possible to realize simple planar sensors, where the appropriate type of modification gives the sensitivity to a certain analyte. The article presents different sensors for environmental parameters monitoring based on modified carbon nanotubes and graphene, including their measured basic electrical parameters and properties.
The paper was presented by Tomas Blecha from Department of Materials and Technology, Faculty of Electrical Engineering, University of West Bohemia, Pilsen, Czech Republic, at the 3rd PCNS 7-10th September 2021, Milano, Italy as paper No.1.4.
Introduction
Nowadays, carbon nanotubes (CNT) are deeply investigated in many applications due to their exceptional properties. These materials can be used to implement basic interconnection structures and create more complex electronic components. Carbon nanotubes can be also chemically modified and thus change their chemical as well as electrical properties. Modification is when CNTs bind other organic or inorganic substances to themselves and thereby change their physical and chemical properties. These modified CNTs are used in the field of passive electronic components and in the construction of organic FET transistors to improve their electrical parameters. Materials based on carbon nanotubes are organic materials, and thus, when applied to environmentally degradable substrates, they enable the realization of biodegradable electronic elements and systems.
Carbon nanotubes have a lot of unique properties. One of them is a large surface and the value of the property can reach 1000 m2/g. This is the reason why carbon nanotubes are good candidates for their use as an active layer in gas sensors development. Their enormous surface represents a lot of space for the interaction of gas molecules. Sensor properties are determined by a sensor active layer. The homogeneity of this layer is key to achieve the highest sensitivity and also affects the other properties of the sensor, therefore, the emphasis on deposition is very high.
The advantage of these materials is that printing techniques can be used for creating functional electronic structures and thus realized flexible and planar electronic elements or entire systems. The easy way to create a thin layer of CNT on the substrate is using wet deposition techniques. There are many methods for creating homogenous layers. Two main requirements for the deposition method selection are firstly thin layer creation and secondly the possibility of a mass production implementation. Thin layers have some advantages in comparison to thick ones. Thin layers are much more homogenous than thick layers. This fact leads to higher sensitivity. The next advantage of the thin layer is the rate of charge transfer from the surface to the gold electrodes. The faster charge transfer improves the dynamic properties of gas sensors such as response and recovery times.
Stable and homogenous CNT dispersion preparation is a challenge for scientists who want to work with this material in a liquid state. There is a big problem with thin films deposition of CNT by conventional deposition techniques (dip coating, drop coating, spin coating etc.) because the used solvent evaporates very slowly. Due to it the “coffee rings” are created during the layer forming. That leads to carbon nanotube agglomeration. The methods that can achieve very thin layers are suitable, not only because of the high conductivity of carbon nanotubes but also because of the efficient and fast transfer of charge from the surface of the layer towards the electrodes. A more efficient charge transfer results in faster sensor response. We used a special and quite new printing technique for the creation of a thin and homogenous layer from carbon nanotube dispersion on the flexible substrate, called the Aerosol Jet System (AJS). Carbon nanotubes can be so deposited on different substrates with the different topology of electrodes (Fig. 1).
references [1], [2], [3], [4], [5]
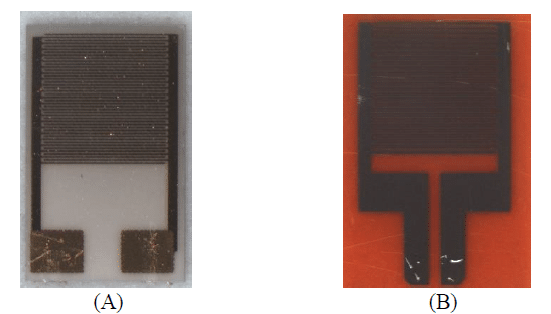
SENSORS FOR ENVIRONMENTAL PARAMETERS MONITORING
Carbon nanotubes are very suitable material for sensitive layers of environmental parameters monitoring sensors such as dangerous gases, relative humidity and temperature. Defects in the CNT structure make it possible to modify with other materials and thus extend the detection capabilities to other analytes. The advantage of these modified CNTs is that chemoresistive sensors can be realized. It means the change of resistance or impedance of these sensors is due to analyte action. Thus, the evaluation electronics for these sensors can be very simple and the whole sensor system is suitable for integration into the Internet of Things system (IoT) because of low power consumption. If the carbon nanotubes are modified by suitable substances some parameters of these realized sensors can achieve better parameters such as sensitivity and selectivity.
NO2 sensors
Nitrogen dioxide (NO2) is characterized as a toxic gas that can damage human health at low concentrations. Electrochemical, resonance, optical and chemoresistive sensors are most commonly used to detect nitrogen dioxide gas. The active layer of these sensors is mostly made of metal oxides (SnO2, WO3, etc.). The disadvantage of these sensors is the need for heating at high temperatures (from 300 °C to 800 °C) to achieve the desired sensitivity and selectivity. Another disadvantage is using expensive deposition technologies such as vacuum deposition processes to create active layers of sensors. These disadvantages are partially removed by chemoresistive sensors with conductive polymer sensitive layers, but they are susceptible to environmental influences (humidity, UV radiation, etc.). The result is gradual degradation that leads to instability of the sensor. A possible solution can be found in composite materials, a combination of conductive polymers with other materials (e.g. Carbon NanoTubes – CNT). CNT, due to their properties, allows them to increase the long-term stability of the final active layer.
Eight different types of MWCNT modification by metal-phthalocyanines were tested and measured. The overview of all tested materials is shown in Table 1. Sensors were tested in the hermetic man-made chamber under the 10 ppm NO2 concentration. This concentration corresponds to the highest permissible concentration in the working environment, also known as PEL (permissible exposure limit). The measurement conditions within the measuring chamber corresponded to the normal laboratory environment. The inside temperature was set to 22 °C, relative humidity 40 %, and gas flow rate 1 litre per minute. This setting simulates the common environment conditions where the sensors could potentially work.
The MWCNT-COOH PbPc(COONa)8 has a much better response to NO2 than pure carbon nanotubes. The sensor resistance dropped by more than 50 % of its absolute value during exposure to nitrogen dioxide. The response shows a very high sensitivity to this analyte (Fig. 3). The rapid resistance stabilization of the sensitive layer at the constant NO2 detection value is another feature improved by the modification and the partial spontaneous desorption of gas occurs. As a result of the desorption, the resistance almost always returns to the same value. This phenomenon eliminates the trend of resistance increase in the individual measurement cycles. Generally, this modification of the CNT leads to the improvement of all important features of the sensor.
references [1], [6], [7]
NH3 sensors
Ammonia is a colourless, very pungent and toxic gas. Ammonia is alkaline in nature, lighter than air and has a negative effect on human health, especially in higher concentrations, which, however, do not normally occur in the air. Inhalation of high concentrations, or even pure gases, leads to serious health problems (mucosal burns) and can even cause death. Commercially available sensors use the electrochemical principle. Using modified carbon nanotubes, it is possible to implement a chemoresistive ammonia sensor.
The carbon nanotubes from Brewer Science company were used for the creation of a thin sensitive layer on the interdigital electrodes by AJS. Before printing the water dispersion of these CNT contain 75 % single-wall carbon nanotubes (SWCNT) and 25 % multi-wall carbon nanotubes (MWCNT) was prepared. The surface of CNTs was covered by molecules of pyrene for better long-term stability. The carbon nanotubes were printed by the Aerosol Jet System on the flexible substrate. The deposited layer underwent optical inspection by scanning electron microscopy. In Figure 3 detail of carbon nanotubes net is shown. This Figure confirms the assumption that CNTs do not create any agglomeration when are printed by the Aerosol Jet System.
The sensors were exposed to ammonia and tested. The test was carried out at room temperature (21 °C) and relative humidity of 40 %. These conditions should simulate a common working environment of the sensor. Ammonia concentration was set at 50 ppm during the sensor testing. This level of concentration follows the maximum exposure limit that cannot be exceeded to avoid harm to human health.
The sensor showed high sensitivity to ammonia (Fig. 4). The resistance increases approximately by 25 % during the gas exposure at room temperature. The response of the sensor to ammonia is different from the response to nitrogen dioxide. The effect of ammonia increases the resistance of the sensitive layer based on CNTs, while the effect of nitrogen dioxide decreases the resistance.
references [8]
Temperature sensors
Reduced graphene oxide is very often used for temperature sensors, which can be easily prepared and deposited on electrode structures. Again, interdigital electrodes are used as the electrode structure, but it is possible to use any other arrangement of electrodes. The graphene-based sensitive layer can be applied to the electrode structure by deposition techniques such as spraying, spin coating or AJS. The evaluation of the measured values is again performed on the basis of the change in electrical resistance. These sensors show good sensitivity to temperature changes from 10 °C to 90 °C, but their problem is their sensitivity to humidity. If the sensor operates in different conditions, where the humidity changes, the absolute resistance values also change due to humidity. Figure 5A shows significant changes in the resistance of the reduced graphene-based sensitive layer as a function of temperature. These changes are large enough and therefore very easy to evaluate. Graphene-based temperature sensors also show good long-term stability and repeatability (Fig. 5B). The advantage of these sensors is that a flexible temperature sensor can be implemented, which can be completely degradable.
Relative humidity sensors
The relative humidity is one of the most monitored environmental parameters. Humidity sensors essentially consist of three main parts, which include a carrier substrate, an electrode system and a sensitive layer. The carrier substrate is a carrier pad made of non-conductive material, on which the electrode system and the sensitive layer are implemented. The sensitive layer is a layer that covers the electrode system and interacts with the target analyte while changing its physical or chemical properties. Materials based on Cu, Zn, W, and ferrite can be used for application in the sensitive layer.
The electrical resistance of carbon nanotubes depends on the change in relative humidity. Therefore, these materials can be used as relative humidity sensors. However, the sensitivity of pure carbon nanotubes to moisture is not significant (Fig. 6A). The resistance change is very small for evaluation. However, in the case of a suitable modification, there is a significant increase in sensitivity by several tens of percents. Another indisputable advantage of these sensors is that their response to changes in relative humidity can be measured by a DC signal. The evaluation circuits are thus significantly simplified. Figure 6B shows the change in electrical resistance due to the change in relative humidity of the sensor with the sensitive layer of MWCNT modified by the COOH group.
Conclusions
Carbon allotropes, especially carbon nanotubes and graphene, are very promising materials for use in electrical engineering. In particular, their application in sensors of environmental parameters makes it possible to implement simple chemoresistive sensors that are at the same time environmentally friendly both in terms of ecological degradability and in terms of low energy consumption. By suitable modification of carbon nanotubes, targeted sensitivity to the monitored analyte can be achieved, and the above research results of these sensors thus demonstrate their functionality. Another goal in this area is to make further modifications to these materials so that they can be used to detect, for example, explosive gases and carbon monoxide. These sensors are currently very robust, energy-intensive and require complex evaluation circuits.
Acknowledgement
This work was supported by European Regional Development Fund; OP RDE; Project: “Carbon allotropes with rationalized nanointerfaces and nanolinks for environmental and biomedical applications” (CZ.02.1.01/0.0/0.0/16_026/0008382).
References
[1] Wang, Chengxiang, Longwei Yin, Luyuan Zhang, Dong Xiang a Rui Gao: “Metal Oxide Gas Sensors: Sensitivity and Influencing Factors“. Sensors [online]. 2010, 10(3), 2088–2106. ISSN 1424-8220. Available from: doi:10.3390/s100302088
[2] Ong, Yit Thai; Ahmad, Abdul Latif; Zein, Sharif Hussein Sharif :“A review on carbon nanotubes in an environmental protection and green engineering perspective”. Braz. J. Chem. Eng. [online]. 2010, vol.27, n.2, pp. 227-242.
[3] A. Peigney, C. Laurent, E. Flahaut, R. R. Bacsa, and A. Rousset: “Specific surface area of carbon nanotubes and bundles of carbon nanotubes,” vol. 39, pp. 507–514, 2001.
[4] Wang, Qiguan a Hiroshi Moryiam: ”Carbon Nanotube-Based Thin Films: Synthesis and Properties”., In: Carbon Nanotubes – Synthesis, Characterization, Applications[online]. InTech, 2011-07-20
[5] Y. Y. Huang and E. M. Terentjev: “Dispersion of carbon nanotubes: Mixing, sonication, stabilization, and composite properties,” Polymers (Basel)., vol. 4, no. 1, pp. 275–295, 2012
[6] T. S. Sri, J. R. Prasad, and Y. Vijayalakshmi: “A review on the state of art of Internet of Things,” vol. 5, no. 7, pp. 189–193, 2016
[7] Stulik, J. and Blecha, T.: “Modified CNTs for NO2 detection“. in 2018 7th Electronic System-Integration Technology Conference (ESTC), Sep. 2018, pp. 1–4. doi: 10.1109/ESTC.2018.8546501
[8] Stulik, J.; Hamacek, A.: “Carbon nanotubes ammonia sensor printed by Aerosol Jet System“. 1st PCNS Passive Components Networking Days, 12-15th Sep 2017, Brno, PCNS2017 Proceedings Pg.91-94, ISBN: 978-80-905 768-8-9