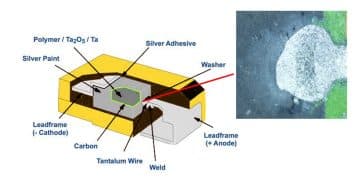
This article is written by Vladimir Azbel Ph.D., semiconductor process reliability engineer consultant, Israel, who investigates how welding of tantalum wire to tantalum capacitor pellet can be optimized to improve its quality and reliability.
Introduction
This study addresses the critical role of welding in the production of tantalum capacitors, focusing on the Heat-Affected Zone (HAZ) formed during the process. Optimizing welding parameters, especially contact force, is essential for minimizing HAZ size, but assessing contact force is challenging.
The proposed method advocates using the pellet’s yield strength to determine optimal contact force, thereby enhancing efficiency and reducing time and material losses. Materials with higher yield strength enable increased welding current and reduced welding time, resulting in smaller HAZ and improved joint quality.
Plasticity, particularly in materials above 5-7%, influences deformation and destruction risk during mechanical and thermal stresses. The study aims to estimate contact force based on yield strength and plasticity, emphasizing the correlation between higher yield strength and a significantly smaller HAZ. Adequate mechanical characteristics are crucial for high-quality welded joints, aligning with the formation process. Managing thermal stresses is essential to prevent deformations and cracks. The paper concludes by proposing the use of a virtual anode calculation program to determine optimal parameters for welding and formation processes, balancing yield strength and plasticity.
Enhancing Tantalum Capacitor Reliability: A Comprehensive Analysis of Yield Strength and Plasticity in Welding Processes for Optimal Manufacturing
In the production of tantalum capacitors (TC), there is a crucial component of the design without which the process is impossible – a sintered tantalum pellet with a tantalum wire lead. This lead can be inserted into the pellet during pressing and then sintered or welded to the already sintered pellet.
Welding the lead to the sintered tantalum pellet is a critical stage in the TC manufacturing process, and the reliability of the final product largely depends on the quality of this step.
In the welding method used, the connection between the pellet and the lead is achieved by melting the wire after it is forced against the pellet. The material around the lead is subjected to heat, leading to a change in its structure in the welding area. This area is called the Heat-Affected Zone (HAZ).
Structural changes in the pellet occur in this region (see Figure 1a, b, c), which can affect the properties of the anode, whose shaping process is conducted through the lead.
The size and type of HAZ structure can serve as a visual indicator of the thermal impact of the welding process, as it reflects the extent of structural changes in the pellet compared to the rest of it.
Reducing the size of the HAZ depends on optimizing parameters, both equipment settings and factors directly responsible for welding quality. The latter includes the current magnitude and duration, the contact force between the lead and the pellet, and other factors discussed in the paper. /1 /
Among these three parameters influencing the quality of welding, assessing the contact force is the most challenging, unlike the current and time, the values of which can be estimated by calculation if the wire diameter and its length extending from the electrode are known.
The magnitude of the contact force should ensure minimal resistance to current flow at the wire-pellet boundary, without causing the pellet’s destruction. The correct choice of the contact force determines the optimal values of the welding current, welding time, and the quality of the welded joint.
The contact force during welding is the pressure applied by the wire on the pellet and must be sufficient to establish good contact between them for the welding process. The magnitude of this pressure depends on the mechanical properties of the sintered pellet, especially its yield strength and plasticity/2,6 /. The yield strength determines the material’s ability to resist deformation and fracture under mechanical and thermal loads. The higher the yield strength, the higher the contact force/pressure can be applied. The high plasticity of the pellet material allows for increased contact force, ensuring wire penetration into the pellet without the risk of its destructive or significant changes.
Today, determining the optimal contact force during spot welding is typically achieved through experimental means based on experience and knowledge. This approach to choosing the contact force is associated with time and pellet loss.
As an acceptable contact force value for welding setup, it is proposed to use the yield strength of the pellet. Knowing the yield strength of the pellet and the cross-sectional area of the wire (depending on the wire undercut angle), the contact force can be calculated, and the wire feed mechanism can be set accordingly using a tensiometer.
From the literature, it is known that the yield strength and plasticity of materials involved in the welding process have an impact on the quality of the welded joints and, consequently, the size of the Heat-Affected Zone (HAZ):
- Increasing the yield strength allows for increasing the welding current and reducing the welding time, leading to a smaller HAZ and, consequently, a higher-quality joint. Conversely, reducing the yield strength can lead to material failure during welding.
- Materials with good plasticity (above 5-7%) can deform more easily, making welding easier and reducing the risk of destruction during the relaxation of thermal stresses.
If the materials to be welded do not have the required yield strength and plasticity values, it can be challenging to find or achieve the optimal balance between contact force, welding current, and welding time to minimize the size of the HAZ, even for an experienced.
Laser welding does not require contact pressure, as is the case with spot welding, but the mechanical characteristics of the sintered pellets remain equally important in laser welding. Therefore, when designing new capacitor designs in which the leg-to-pellet connection is achieved through welding, it is crucial to consider the mechanical characteristics of the sintered pellet.
The aim of this study is to utilize the yield strength and plasticity of the sintered tantalum pellet, obtained through powder pressing and sintering, to estimate the contact force. This approach can help reduce time and material losses when optimizing welding current and time for high-quality welds, which correlates with reducing the size of the Heat-Affected Zone.
The influence of yield strength and plasticity on the Heat-Affected Zone is illustrated by the data presented below.
In the Figure. 2 below, a comparison of the appearance of the welds on two pellets (labeled “A” and “B”), differing in compaction density and sintering temperature to achieve different yield strength values, is shown to analyze their effect on the Heat-Affected Zone.
The welding of the lead to the pellet, as discussed in this study, was conducted using the method described, on the equipment (see Appendix) in the referenced work /1 /.
Increasing the compaction density and sintering temperature in pellet “B” compared to pellet “A” allowed an increase of 40% in the yield strength of pellet “B” compared to “A.”
Metallographic analysis of the Heat-Affected Zone conducted on the cross-sections of pellets “A” and “B” (see Figure 3) illustrates that pellet “B,” (see Fig. 3B, B1) with a higher yield strength, has a significantly smaller Heat-Affected Zone compared to “A.” (see fig. 3A, A1).
Based on the above, it becomes evident that without sufficient mechanical characteristics of the sintered pellet, such as yield strength and plasticity, it is challenging to guarantee high-quality welded joints even with the necessary welding experience.
The magnitude of the yield strength and plasticity of the sintered pellet, ensuring quality welding, should be acceptable for the formation process as well. This is due to the similarity of physical processes related to the material’s ability of the sintered pellet to relax thermal stresses arising during welding and formation. Understanding and managing thermal stresses are crucial aspects of these processes to prevent deformations and cracks, ensuring acceptable welding and formation.
To determine the optimal parameters that combine the values of yield strength and plasticity suitable for both welding and the formation process, we will use a virtual anode calculation program /3,4 /.
Conclusion:
This paper underscores the critical importance of optimizing tantalum capacitor manufacturing by analyzing yield strength and plasticity in welding processes, with a particular focus on the Heat-Affected Zone (HAZ). The proposed method introduces a novel approach to assess contact force during welding, using the pellet’s yield strength for more calculated parameter determination, thereby reducing time and material losses. Higher yield strength materials contribute to increased welding current, reduced welding time, smaller HAZ, and improved joint quality.
The study emphasizes the pivotal role of adequate mechanical characteristics, specifically yield strength and plasticity, in achieving high-quality welded joints. Comparative analysis of welds on pellets with varying press density and sintering temperature confirms that higher yield strength results in a significantly smaller HAZ, reinforcing the importance of these properties in welding.
Acknowledging the challenges in assessing contact force, the paper’s proposal to use the pellet’s yield strength as a basis for determination provides a practical and efficient solution. Metallographic analysis demonstrates that higher yield strength materials lead to a substantially smaller HAZ, validating the proposed method and highlighting the need for suitable mechanical characteristics.
The research recognizes the importance of mechanical characteristics even in contactless processes like laser welding. The proposal to use a virtual anode calculation program for optimal parameters underscores the commitment to efficiency and precision in the manufacturing process.
In conclusion, this research offers valuable insights into optimizing tantalum capacitor manufacturing by aligning welding parameters with the mechanical characteristics of the sintered pellet. The proposed method not only enhances welding efficiency but also holds promise for improving overall reliability and quality in tantalum capacitors.
Reference
- Method of Welding Tantalum Lead Wires to Tantalum Capacitor Anodes U.S. Patent, 4,319,118, 1982
- Quality control sinter pellet an anode, Ta- capacitor, by Mechanical testing V. Azbel on LinkedIn
- New Approach to Tantalum Capacitor Anode Design, V. Azbel EEE passives components
- Virtual program for calculating the risk of overheating in the manufacture of the anode of a tantalum capacitor. V. Azbel Passives Components
- A new approach to anode tantalum capacitor production V.Azbel https://passive-components.eu/new-approach-to-tantalum-capacitor-anode-design/
- Tantalum Capacitors Reliability, Leakage Current Stability Prediction and Cost Reduction by Anode Characterization During Manufacturing Process; Vladimir Azbel 3rd PCNS Passive Components Networking Symposium 7 – 10TH SEPTEMBER 2021, MILANO, ITALY https://passive-components.eu/tantalum-capacitors-reliability-prediction-by-anode-characterization-during-manufacturing-process/
Read the original post at Optimizing Tantalum Capacitor Manufacturing Through Yield Strength and Plasticity Analysis in Welding Processes