As the world shifts towards a more sustainable and efficient future, SiC is playing an increasingly important role in the development of EVs. This blog article is based on RCD Advisors Insights post and its expertise. Published by EPCI.eu under RCD permission.
The demand for electrification is a bright spot in the tech hardware industry during the current downcycle. Soaring electric vehicle (EV) shipments for the last three years have compelled forecasters to bump up sales projections for the rest of the decade.
According to Goldman Sachs, by 2035, EVs will rise from roughly 10% of global sales in 2022 to 50% by 2030. This optimism is paving the way for aggressive forecasts in electrification hardware, semiconductors, and other electronic components.
To achieve this forecast, though, EVs must move from a niche to the mainstream. It won’t be all rainbows and sunshine. In December 2022, just before announcing his retirement, Toyota President Akio Toyoda publicly expressed skepticism about pursuing an all-electric vehicle strategy.
Then in January, Tesla warned of lower profit margins and increased “uncertainties” in the market. The company has responded to its excess production with aggressive price cuts. There are signs that even in China, the world’s largest EV market, the ending of subsidies may affect EV demand.
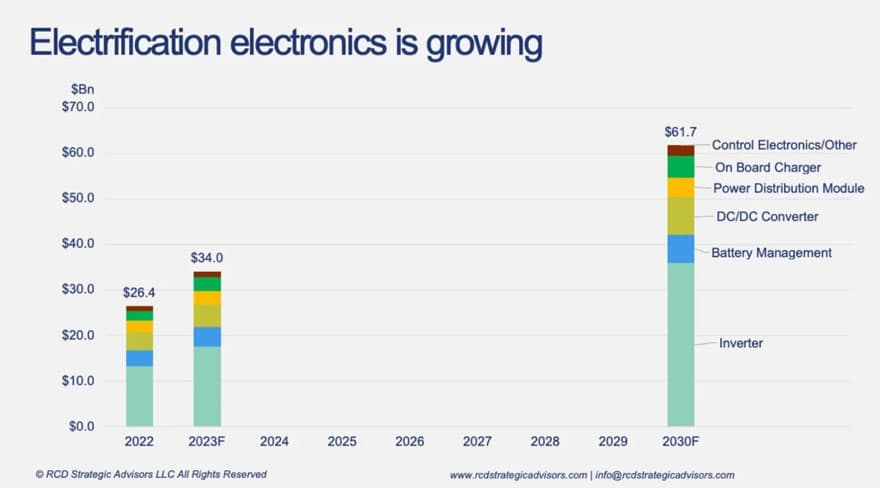
To this point, the majority of electric vehicle (EV) sales have been concentrated in the high-end and low-end market segments; in 2022, around 60% of EV transactions featured a base cost of more than $50,000 or less than $20,000, while for internal combustion engine vehicles (ICE) this figure was closer to 30%. Buyers in the high-end segment are willing to pay extra for superior performance or luxury, and those at the low-end are willing to sacrifice driving range for a lower price.
However, in the mainstream market, the price-performance balance must be carefully weighed in order to achieve the best value. As Tesla stated in their recent Investor Day event, cost reduction is essential in order to facilitate the shift of EVs to the mainstream. Despite this progress, the EV industry still has a long way to go.
The focus on cost reduction will pass through to the supply chain. As a result, pricing pressures will mount as automotive electronic supply chains recover from supply/demand imbalances. Furthermore, for the rest of the decade, the efforts of western governments to regionalize and duplicate critical supply chains (like semiconductors) will only add to this downward pricing pressure (overcapacity). This pricing pressure will likely rein in value growth for the electronics industry. It is fundamentally why this consultancy is skeptical of some of the published growth forecasts for semiconductors.
Nowhere will cost pressure impact the semiconductor market more than in the adoption of SiC-based power semiconductors. SiC is a semiconductor material that has unique advantages in power applications. EV power inverters that use SiC-based semiconductors are much more efficient than silicon-based designs. The higher efficiency can translate into lower thermal management requirements and higher power density (i.e., increased performance).
SiC has attracted interest as a novel semiconductor material since the 1980s and was first commercialized as a Schottky diode by Infineon in 2001. The benefits of SiC for EV applications were well-known in the 1990s. Tesla achieved a significant milestone in 2018 when it incorporated STMicro’s SiC power MOSFETs in the Tesla Model 3 inverter. That commercial breakthrough was a long time coming.
SiC technology offers a number of advantages over traditional silicon components, such as higher power density and faster switching speeds. This means that EV components built with SiC can run cooler, more efficiently, and with greater reliability. SiC technology is being used to create more efficient power converters, allowing for the efficient transfer of energy between the battery and motor. This improved efficiency can lead to greater range and performance for EVs.
The consensus is that Tesla paved the way to broader adoption. Wolfspeed estimates that 60% of all BEVs will use SiC by 2027. In 2021, investment bank Canaccord Genuity estimated that silicon carbide wafer (150mm equivalents) capacity will increase from 125k in 2021 to more than 4 million in 2030 to meet the demand for the EV market. Wolfspeed, Infineon, STMicro, onsemi, Mitsubishi Electric, and Rohm have all announced plans to expand SiC capacity to meet these needs.
But Tesla’s comments during its Investor Day event may paint a more nuanced outlook. Powertrain engineering leader Colin Campbell disclosed that their next-generation drive train unit would use up to 75% less SiC. As is usually the case with Tesla’s “pre-” announcements, the presentation lacked details. Mr. Campbell suggested that Tesla had designed a novel power semiconductor package with better heat dissipation, enabling the reduction in die area.
Since then, many market research firms, financial analysts, engineering firms, and pundits have enjoyed speculating how Tesla achieved such a breakthrough. You can read some theories here, here, here, and here. There is no need for further speculation, but it is worth pointing out that Tesla claimed they could reduce the semiconductor content with better thermal management materials and package assembly processes. So, what may seem like a design loss for SiC technology could be a win for other parts of the electronics supply chain.
As the Tesla announcement suggested, much can go wrong with the SiC/EV growth story. But this shouldn’t be a surprise in the context of the 20-plus years of SiC commercialization history. Until now, SiC has been adopted only in premium EVs where power density and performance are highly valued. The list below identifies EVs that have adopted SiC-based power electronics.
- Tesla Model 3, Model S, and Model Y
- Lucid Air
- Hyundai/Kia EV6 Gt
- Mclaren Applied
- BYD Han
- Toyota Mirai (Fuel Cell)
- Porsche’sPorsche’s Taycan
Note: All major suppliers of SiC are touting design wins in future vehicle platforms. But most are confidential, and assessing how many platforms are premium vs. mainstream is impossible from those disclosures.
If SiC is part of the future growth in EVs, it will have to win in mainstream designs. For that to occur, SiC must achieve cost parity with Si IGBTs, which are also improving. The problem is that SiC is 3-5x more expensive than Si IGBTs for the equivalent current rating. Using simple calculations, SiC die component price (not cost) is about $0.20/mm2. By comparison, Si IGBT finished die price is less than $0.03/mm2. SiC is expensive because the starting crystal materials are much more challenging to grow. SiC die costs have been exhaustively modeled (See here, here, and here) with many scenarios for possible cost reductions.
And for sure, progress is being made. The investments in capacity expansion and larger wafer sizes will help. But even in the most optimistic models, SiC will always be significantly more expensive than silicon IGBTs. So will SiC always chase incumbent technology?
The alternative way for SiC to achieve parity is to extract cost savings from other parts of the EV powertrain. For example, SiC can reduce inverter thermal management costs and offers an improved driving range, reducing EV battery costs. These cost savings vary considerably by design, and engineers have also modeled these scenarios extensively.
Unfortunately, the scrutiny over Tesla’s comments on “a 75% reduction in SiC usage” masked a more interesting message. Tesla was touting their capability to optimize EVs by coordinating across all parts of the power electronic value chain. In other words, integration is a source of innovation, not just a way to remove stacks of profit margin. It illustrates one of the main prescriptive themes in RCD Advisors’ consulting practices. And if it could work for Tesla, it could work for other suppliers too.
The supply chain for SiC EV was initially formed across specialist organizations. There were merchant crystal growers, merchant power device makers, and merchant power electronic specialists. Merchant markets are optimal when the technology is stable. Specialist suppliers can aggregate information and volume experience across many end customers. This phenomenon creates a virtuous cycle of competition and efficiency.
But, captive (vertically integrated) markets are better when technology is still evolving because there is too much coordination and interdependence among different system components. Moreover, for SiC, it is questionable how much volume experience and information gathering would happen outside the automotive industry. Anyone who has ever forecasted SiC growth knows all too well that EV adoption is the only assumption that matters. EV demand would dwarf other applications. For business development, one would be better off viewing SiC as an automotive component (like a MEMs pressure sensor) rather than an improved version of a generic power semiconductor. So at least initially, it may make more sense for SiC to be supplied through a dedicated vertically integrated automotive supply chain.
The semiconductor industry is littered with examples of downstream vertical integration (handset RF GaAs PA modules, industrial IGBT modules, and, more recently, Nvidia offering AI cloud services). In most of these cases, the downstream process integration diluted margins. But suppliers did it to seed and accelerate the growth of an end market. A dedicated and vertically integrated supply chain may be the only way for SiC to achieve mass market adoption as EVs become mainstream.
It is starting to happen. Leading power semiconductor suppliers have aggressively backward integrated to secure wafer supply. They have also traditionally maintained bare die module packaging capability. But as Tesla has suggested, there may need to be more downstream integration into inverter assemblies as a way for SiC to capitalize to reach cost parity. Tier-one suppliers have begun to move in this direction by forging partnerships. It is the first step.
Another example is Denso, one of the few Tier-one suppliers still fabricating semiconductors. Since 2010, Denso has also been an integrated SiC supplier to Toyota. Denso’s integrated approach, tightly knit with its primary OEM customer, could offer similar advantages to Tesla’s backward integration. But that will only happen if Toyota ever fully hops on the EV bandwagon.
Since electrification and automobile automation emerged, there has been ample hand-wringing over the bargaining leverage of semiconductor suppliers and how the traditional tier-ones may leak value into other parts of the value chain. Tier-ones will only leak value if they stand still. At least for SiC, as Tesla has suggested, there is an opportunity for suppliers willing to bet on capturing technology innovations across supply chain levels. The strategy merges bare-die SiC into system-level functions that improve thermal management and efficiency (Power SiP).
For SiC semiconductor suppliers, it means forward integrating into inverter assemblies. For Tier-ones, it means backward integrating into SiC supply. The alternative is to relegate power SiC back to the niche market it has always been and allow incrementally improving silicon IGBTs to capture the lion’s share of the price/performance segments.
The potential of SiC technology is not limited to EV applications. SiC can also be used to build more efficient and powerful solar panels, allowing for more efficient energy generation. It can also be used to build electric vehicle chargers, allowing for faster and more reliable charging times.
Understanding linkages across electronic industry value chains is fertile ground for mining future innovations. RCD Advisors can help organizations in the tech hardware space understand those opportunities. Contact us to learn more about the practice.