This article discusses the safety capacitor standards and requirements for EV and power electronic applications and how ceramic capacitor advancements can answer the latest trends.
The paper was presented by Moaz A. Elghazali, Murata Electronics Europe at the 4th PCNS 10-14th September 2023, Sønderborg, Denmark as paper No. 5.5.
Abstract
New developments and increased applications with high power require special EMI suppression capacitors for connection to supply mains. Specifically, Y-Capacitors are used for filtering in “line-to-ground” applications where a failure could lead to an electrical shock. Different challenges are given such as requirements through safety standards, electrical performance, reliability as well as component size. Ceramic capacitor technology can provide solutions for these requirements by reducing the number of components, miniaturization, increase performance by offering different solutions for various challenges in power electronics applications.
Introduction
Technological developments in power electronics continue to disrupt different industries from automotive to photovoltaics at an unprecedent pace. For example, the automotive industry witnesses a revolutionary advancement driven by the rapid development of electric vehicles (EVs). What took the internal combustion engine more than a century to mature, was ramped up for the electric motor in much shorter timescale. [1] Nevertheless, this pace of EV development imposes challenging technological demands to the power electronics that enable EVs.
One of the main challenges in the automotive industry is to enable EVs to travel longer distances and to shorten the charging time in order to increase EV adoption. To achieve these goals, a key factor is to extend the operating voltage of the EV battery Packs from 400-450 V DC up to 800V and 900V DC. Doubling the pack voltage from the one hand reduces the needed current by factor of 2 and from the other hand reduces the I2R energy losses by factor of 4. Besides reducing losses, lowering current enables reducing the wiring looms’ space and weight, which decreases the overall vehicle mass and extends the travel range. In addition, the high voltage packs improve the charging station efficiency and cut down energy losses. [2]
High voltage design of a battery pack imposes high operating voltage rating on different electronic component including capacitors. Battery packs are made up of hundreds of individual cells, each producing around 4V when fully charged, wired in series to produce the requisite pack operating voltage. It’s the design of the pack, and the battery management system (BMS) that controls how each cell in it is charged and discharged, which enables faster charging. [3] Availability of key components, such as safety capacitors with high enough operating-voltage ratings is vital to implement it in the design and meet automotive demands as well as high safety requirements.
Safety Capacitor for Automotive Applications
Safety capacitor is used for common mode filtering and isolation purposes. It is found in different EV powertrain applications such as Battery management system (BMS), on board charger (OBC), DC-DC converters, and traction inverters. Safety capacitor is used either across the AC line (called X capacitor) or connected to the common mode (i.e., the car’s chassis) (the capacitor is called Y capacitor in this case). [4,5]
Figure 1 (below) shows the use of safety capacitors in an onboard charger, with two devices (CY1 and CY2) acting as Y capacitors in the primary side of the circuit, two more (CY4 and CY5) taking the same role in the secondary, a two more pairs (CY6 and CY7) performing the same function for the battery (CY6 and CY7) and the traction inverter (CY8 and CY9). Capacitors CX1 – 4 perform smoothing functions throughout the powertrain.
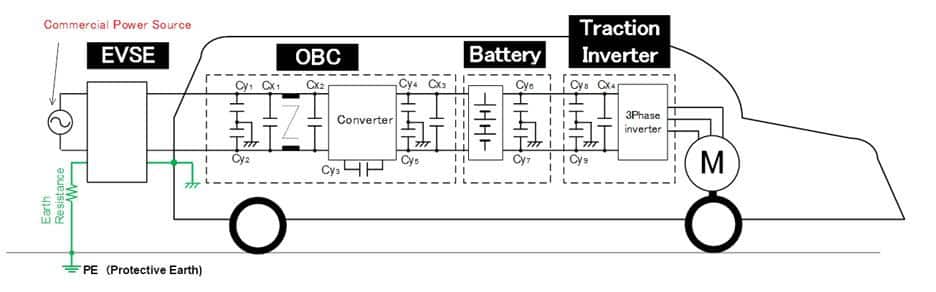
There are different technologies used for safety capacitors. Traditionally, through-hole mounting capacitors such as film capacitors or lead type disc ceramic capacitors are used. Nevertheless, through-hole mounting devices are bulky and vulnerable against vibrations. On the other hand, surface-mountable multilayer ceramic capacitors (MLCCs) have advantages such as better reliability in case of vibrations, saving space or height, efficient production procedure, and better EMC performance.
Safety capacitors must meet several standards. The standard automotive AEC-Q200 quality standards, safety capacitors must also follow safety standards such as IEC60384-1 and IEC60664-1. This sets different strict requirements such as withstanding a peak impulse of 5 kV, AC/DC bias stress tests as well as requirements on creepage distances against the applied voltage. [6]
To address these issues, Murata has developed a range of surface-mountable multilayer ceramic capacitors (MLCCs) with peak DC operating voltages of 1500V and peak AC operating voltages of up to 305Vrms.
The EVA capacitors offer a creep distance of 6 and 10mm, making arcing less likely than in other devices with creep distances of just 4mm. Using Murata’s EVA parts also saves PCB area and assembly costs and should improve manufacturing yields.
The high DC and AC operating voltages of the parts give them the headroom to work in today’s EV drivetrains, and to take a role in an emerging class of vehicles that are using 800V DC and 900V DC battery packs to reduce resistive losses.
The EVA devices join Murata’s range of safety capacitors, which includes the DE6 parts offered in a through-hole mounting package and the surface-mountable KCA parts, which have a creepage distance of 4mm. Although the EVA parts are longer to accommodate the increased creepage distance, they retain the mechanical strength of the KCA parts because they have metal terminations and an internal design that focuses on electrical strength. This provides a range of Y- capacitors that satisfies the safety standard for automotive as shown in table 1.
Safety Capacitor for General Industrial Applications
Safety capacitors are needed for a wide range of industrial applications such as consumer electronics, automation, energy generation, etc.
For example, the energy market has been changing rapidly to achieve more environmental-friendly energy generation solutions. In this context, solar inverters, DC house concept, and Heat pumps are applications that proved to offer efficient solutions to the environmental energy concerns the as well as the rising prices in the energy market.
The concept of the DC House is, to use Green Energy, provided from solar panels or wind turbines. Energy generated from these renewable sources are in DC Voltage, however, devices inside houses require AC Voltage. For this power conversation, inverters must include safety capacitors for protection against pulses that can cause electrical shocks. Table (2) shows a classification of the Y caps used various general industrial applications.
Summary and Conclusions
The Y-capacitors are essential building block in power electronics applications to enable new innovations for electric vehicles as well as Photovoltaics and other general industrial applications.
The Y capacitor provides protection for people and devices against potential electrical shocks. Therefore, the Y-capacitor technology requires robust manufacturing process to meet strict safety standards.
The new Molded-type EVA type capacitor brings more robustness to the Y-capacitor enabling longer creepage distance and higher withstanding of impulse voltage.
REFERENCES
[1] Hoeft, F. (2021). Internal combustion engine to electric vehicle retrofitting: Potential customer’s needs, public perception, and business model implications. Transportation Research Interdisciplinary Perspectives, 9, 100330.
[2] Zwicker, M. F. R., Moghadam, M., Zhang, W., & Nielsen, C. V. (2020). Automotive battery pack manufacturing–a review of battery to tab joining. Journal of Advanced Joining Processes, 1, 100017.
[3] Pattipati, B., Pattipati, K., Christopherson, J. P., Namburu, S. M., Prokhorov, D. V., & Qiao, L. (2008). Automotive battery management systems (pp. 581-586). IEEE.
[4] Zhai, L., Hu, G., Song, C., Lv, M., & Zhang, X. (2021). Comparison of two filter design methods for conducted EMI suppression of PMSM drive system for electric vehicle. IEEE Transactions on Vehicular Technology, 70(7), 6472-6484.
[5] Safayet, A., & Islam, M. (2019, March). Modeling of conducted emission for an automotive motor control inverter. In 2019 IEEE Applied Power Electronics Conference and Exposition (APEC) (pp. 1265-1272). IEEE.
[6] Roberts, S. 2021, August, Overvoltage Categories in Power Supply Systems, EE Power. Overvoltage Categories in Power Supply Systems – Technical Articles (eepower.com)