by Jean Pascal Michelet and Jean Edmond Le Calvé
VALEO Créteil, France
submitted to the 2nd PCNS 10-13th September 2019, Bucharest, Romania as paper 4.4.
Introduction
Some PCBAs were submitted to a whisker test +85°C 85% RH for 200h duration and additional 2h from +85°C/85% RH-T° +25°C/50% RH 5 Cycles. The functional test pass and boards were sent to an external lab for visual inspection. Inspection failed because of Tin whiskers detected on MLCCs terminations.
As reminder a whisker is a spontaneous columnar or cylindrical filament, usually of monocrystalline metal, emanating from the surface of a finish. In automotive electronic the most common are Tin Whiskers growing on Tin platted Copper surfaces. Our suppliers delivering components with Tin or Tin alloy finishes, if no whiskers mitigation method is used or efficiency demonstrated, should perform whisker tests according to JESD-201 standard / 22A121 method [1] [2].
As many Multi-Layer-Ceramic-Capacitors (MLCCs) got whiskers, we returned to the Bill of Material (BOM) and traceability to find out exactly the part numbers. We went back to their qualifying and the results were good. We also checked the Process Change Notification (PCN) history to see if the suppliers submitted any PCN relative to the termination scheme and we did not find any on this topic. Moreover, all the impacted MLCCs got a Nickel barrier between Copper electrode and Nickel platting supposed to avoid or limit the Tin whiskers growth.
Observations
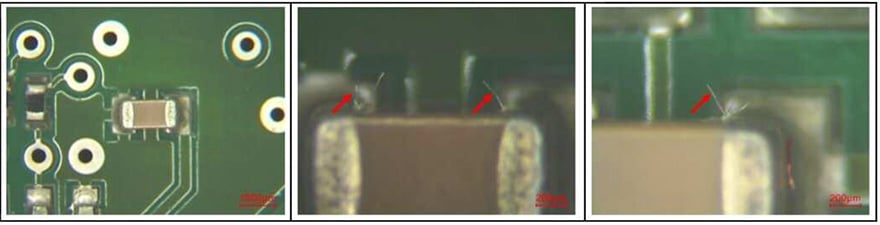
Observations of the whiskers: Lengths are measured up to 225μm. Whiskers have tubular shapes. They are located on the sides only, never on the top (not possible to observe the bottom). Whiskers are located between the Tin platted termination and the flux rise.
The shape of these whiskers is not conventional and is not described neither by the NASA [3] nor by JEDEC [2]. Some hollow whiskers were reported [4], [5], We did not find any document on Tubular whiskers growth on Electronic components. For us it is the first observation of such structure.
MLCC. Bromide origin is unknown
on the MLCCs
Root Cause Analysis
A cross section was done in the horizontal plane of a MLCC at the maximum flux rise where the Whiskers grow.
whiskers. In the section plan the tubular shape is evidenced. Whiskers growth is on the ceramic nearby or in contact
with the Tin edge of Tin layer
polishing artefact. Bromide origin was identified as coming from the Solder Flux
Risk Analysis
The major risk of metallic whisker is to reduce the insulation distance or worst to make a short circuit. In our case the whiskers is made of Tin, Oxygen and Bromide. The visual observation evidenced transparent tubular structure, so it is not a pure metal, but a compound of Tin oxide + Bromide.
Tin oxide is classified as wide band gap (3.6 eV) N-type semiconductor. Considering the risk to have a conductive path, we make electrical verification. We did several attempts to contact the Whiskers by probing but it failed because of whiskers are too brittle. We used a cross section through both MLCC termination solder and some whiskers ends to be contacted with Silver epoxy ink.
Tin tubes growth hypothesis
While lowering the reflow temperature profile, more hollow whiskers were possible to be generated. This suggests that the SnO hollow whiskers growth mechanism is promoted by some still active flux residues not fully desactivated by the reflow process. Among these residues the weak organic acids (WOA) and halogen/bromine are suspected to contribute to the growth mechanism of SnO whisker.
Tin hydroxide chloride [Sn3O2(OH)2-xClx] was reported to be intermediate corrosion products on reaction from Sn to SnO/SnO2 (depending on pH and presence of chlorine halogen) [7]. A similar Tin hydroxide bromide could have been the intermediate corrosion product to give rise to the tin oxide hollow whisker encountered:
This localized corrosion process in presence of halogen ion (bromine) could have been at the origin of the tube shape observed. The transformation of Tin nanowires to amorphous oxide nanotubes has been described by HoSun Shin [8] based on a localized corrosion process in an aqueous solution involving hydrochloric acids (from halogen chlorine ion). The nano-tubes were formed by the dissolution of the tin atoms in the core of the “nanowire” while the tin oxide shell was remaining.
Conclusion
Hollow Tin Wiskers are transparent, very brittle and not conductive.
We demonstrated no risk of leakage or short circuit. At visual inspection they can be considered as cosmetic.
Growth mechanism is supected to come from a localized corrosion process by a Bromine acidic solution from the Solder flux residues and the moisture from the humid atmosphere of the damp heat test.
References
1) JEDEC STANDARD JESD22-A121A “Test Method for Measuring Whisker Growth on Tin and Tin Alloy Surface Finishes”, July 2008.
2) JEDEC STANDARD JESD201A “Environmental Acceptance Requirements for Tin Whisker Susceptibility of Tin and Tin Alloy Surface Finishes”, Sept. 2008.
3) Jay A. Brusse, Gary J. Ewell, and Jocelyn P. Siplon, “Tin Whiskers: Attributes and Mitigation”, CARTS 2002: 22nd Capacitor and Resistor Technology Symposium, 25-29 March 2002
4) H. Kehrer and H. Kadereit, “Tracer Experiments on the Growth of Tin Whiskers,” Applied Physics Letters, 16, no. 11, pp. 411-412, June 1, 1970.
5) Jing Cheng, Paul T. Vianco, and James C.M. Li, “Hollow tin/chromium whiskers”, Applied Physics Letters, 96, 184102, 2010.
6) David Hillman, “False tin-whiskers – beware of masquerading tin-copper intermetallics”, ITRI, 2012
7) Pierre Eckold, “Corrosion of Tin and its Influence on Whisker Growth”, 7th IPC–CALCE International ymposium on Tin Whiskers, November 12-13, 2013.
8) Ho SunShin, Seong GiJeon, JinYu, Jae YongSong, “Transformation of Sn nanowires to oxide nanotubes by a localized corrosion process”, Materials Letters Volume 82, 1 September 2012.
Acknowledgements
Special Thanks to José Gomes from ILED. Investigation Laboratory for Electronic Devices Site Montesquieu 8 Allée Isaac Newton 33650 Martillac-France
more 2nd PCNS symposium technical papers can be viewed and downloaded in pdf from EPCI Academy e-Proceedings: