A stable, reliable, and responsible tantalum supply chain is critical to the supply of electronic components such as capacitors and semiconductors for the automotive, aerospace, medical, defense, energy, and chemical processing industries. Until recently, the tantalum supply chain has experienced intermittent periods of stability and volatility.
This paper will discuss tantalum supply chain past, present, and future, and how it can now be truly viewed as sustainable and reliable in support of all relevant industries.
The paper was presented by Gordon Smith, Global Advanced Metals, USA at the 4th PCNS 10-14th September 2023, Sønderborg, Denmark as paper No.2.1.
The 2020‘s have ushered in a new era for the tantalum supply chain. Tantalum ore supply has become more diversified geographically and by mining methodology, with further regulatory-compliant processors situated globally. The increasingly stable ore supply feeding the historically reliable smelters will fundamentally improve overall supply chain stability.
Tantalum Capacitors: From Then to Now
Tantalus, a figure from Greek mythology, punished by Zeus for a transgression to forever be thirsty and hungry while standing in a pool of water with a piece of fruit tantalizingly just out of reach. In 1802, A. Ekeberg, a Swedish chemist, encountered a tantalizingly difficult metal to dissolve in mineral acids, leading Ekeberg to aptly name the new element tantalum.
In the early years, a large driver for tantalum growth was “wet” and “dry” type capacitors. Tantalum metal powder, when voltage is applied, uniquely grows an amorphous dielectric on the powder surface, its thickness directly related to the formation voltage. Wet tantalum capacitors were developed in the 1930’s and dry (aka “solid”) tantalum capacitors were invented by H. Haring, N. Summit, and R. Taylor of Bell Telephone Laboratories in 1953.1 The first generation of solid tantalum capacitors consisted of pressed porous tantalum powder as the anodic material, amorphous tantalum pentoxide (Ta2O5) as the dielectric and manganese dioxide (MnO2) as the cathodic material. Tantalum capacitors volumetric efficiency (i.e., the ability of these capacitors to hold more charge per unit volume compared to competing technologies) found favor in electronic designs as the trends to electronic device and component miniaturization began to accelerate.
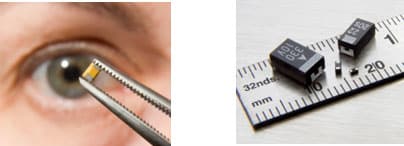
Capacitor manufacturers developed capabilities to make tantalum capacitors in many types to cover various applications. The types of tantalum capacitors range from molded surface mount chip, covering almost 90% of share, to coated chip, radial chip, molded radial, molded axial, hermetically sealed and wet slug.2 Today’s molded surface mount tantalum chip capacitors offer3
- A capacitance range of 0.1uf to 2200+uf
- A capacitance tolerance of +/- 20%, +/- 10%
- Working voltage rating 4V to 100V
- Direct current leakage (DCL) as low as 100nA
- Equivalent Series Resistance (ESR) as low as 4mꭥ
- Operating temperatures of -55°C to 175°C
- Heights down to 1mm
The capacitance of a tantalum capacitor is directly proportional to the porous tantalum powder’s surface area. Tantalum powder producers developed new techniques to increase the surface area for the porous tantalum capacitor grade powder, thus enabling miniaturization and higher capacitance per volume. In parallel to increasing the surface area, tantalum capacitor grade powder producers have discovered new techniques to reduce impurities and improve the powder’s physical properties. This has enabled lower direct current leakage (DCL), enabled higher capacitance-per-volume (CV/cc), lower equivalent series resistance (ESR), and therefore enable increased and further component miniaturization. A broad range of capacitor properties can be achieved by altering the tantalum powder.
The most significant breakthroughs in tantalum capacitor performance were achieved through changes in the cathode material.4 The smaller market of wet tantalum capacitors utilizes a tantalum cathode separated from the tantalum anode dielectric by a liquid electrolyte, typically an aqueous solution of sulfuric acid. The tantalum molded chip capacitor, which carries the more significant portion of the tantalum capacitor market, has two different cathode materials – MnO2 and conductive polymer. MnO2 as the cathode in a tantalum capacitor was introduced in 1953 and accounted for the majority of market demand through the 2010’s before being steadily replaced by conductive polymer technology. Since its introduction, MnO2 as the cathode in a tantalum capacitor has provided high reliability, high stability, and high volumetric efficiency. The conductive polymer cathode was developed in the 1980’s and 1990’s by NEC Corporation in Japan. Polymer tantalum capacitors initially used the polymer mixture of Poly (3, 4-ethylenedioxythiophene) with polystyrene sulfonate (PEDOT: PSS) as the cathode material but tantalum capacitor companies have developed specialty conductive polymers over time to enhance performance. Conductive polymer cathodes offer improved equivalent series resistance (ESR) as well as other capacitor enhancements.
Since the tantalum capacitor was first developed, the tantalum supply chain has evolved to support capacitor demand which today accounts for approximately 40% of annual total tantalum demand. Tantalum capacitor manufacturers continue to push the envelope on miniaturization, design configurations, and packaging to maximize the capacitance per unit volume. The molded surface mount tantalum chip capacitor has been designed for automatic, “pick-and-place” or “Surface Mount Technology” printed circuit board placement. This design is the first choice where volumetric efficiency and/or long-term reliability are essential features in applications such as servers, lap-top and desktop computers, automobiles, handsets, game consoles, military and defense, and even the Mars Rover (where running repairs are not really an option)!
Tantalum Ore Supply: From Then to Now
Before the late 1970’s tin mining was the primary source of tantalum concentrate (ore). Tin deposits would experience financial penalties for tin ores with tantalum present, so tantalum was removed and discarded as waste slag. This resulted in the accumulation of large quantities of low-grade waste tailings and tantalum in slag primarily in Thailand and Malaysia. While now a low volume source, synthetic tantalum concentrates from tin slags continue today as a tantalum supply from these same two countries.
The tantalum supply chain migrated away from tin slags and developed longer term industrial scale (often referred to as “hard rock”) tantalum mines as a primary source for ore concentrate.5 From the late 1980’s hard rock mining of tantalum ore was primarily in Western Australia with other sources in Brazil and Canada. The Western Australian hard rock tantalum sources were primarily from the Greenbushes and Wodgina mines, both still associated with tantalum ore supply.
By early 1990’s, the Western Australian mines invested to increase supply capability, but not fast enough to keep pace with rising demand from the cell phone and internet bubble of 2000. The ensuing shortage caused the CEO of a well-known computer brand to exclaim on a financial broadcast “What is a tantalum capacitor and why can’t I get one!”.
Historically, hard rock industrial scale mining in stable jurisdictions is reliable but relatively costly. Small scale artisanal mining is less costly but can be unreliable depending on local political or economic conditions. By the mid-2010’s artisanal scale mining began to displace hard rock sources as responsible sourcing mechanisms were implemented and therefore traceability concerns alleviated.
A brief introduction of artisanal mining – artisanal mining is small-scale, low or non- mechanized and can be sporadic depending on local economic and political conditions. Tantalum artisanal mining is mostly focused in Central Africa, specifically in the Democratic Republic of the Congo (DRC), Rwanda and Burundi. Artisanal mining occurs in soft rock, alluvial deposits; it’s very nature of being simple and small-scale means that it can be started or stopped quickly according to market conditions.6
The DRC, in particular, has a history of conflict. Before the implementation of a traceability mechanism in the early 2010’s, many downstream tantalum consumers chose to avoid sourcing from the region to minimize risk of such trade financially supporting criminal groups. The implementation of the Conflict Free Sourcing Initiative (CFSI), known today as the Responsible Minerals Initiative (RMI), provided increasing assurance to downstream consumers of tantalum (and also tin, tungsten and gold, collectively known as 3T’s&G). The RMI (along with other organizations and programs such as the ITSCI Program for Responsible Mineral Sourcing) created a comprehensive set of tools and processes to enable the credible implementation of responsible and ethical mining and trade practices in the Central Africa tantalum supply chain. The primary process is rooted in a bag-and-tag system that enables tracing and chain of custody of the material from a specific mine to a smelter/processor.
In December 2010, the Global Advanced Metals (GAM) tantalum processing plants in the USA and Japan were the first of any metal type to be audited and declared “Conflict-Free” by CFSI. Since then, over 40 companies that participate in the tantalum supply chain have been audited and confirmed compliant to the regulatory and industry conflict-free standards. Achieving this level of industry conflict-free compliant participation is costly, but opens markets for sale of material from this region, benefiting artisanal miners and their communities.
Tantalum Supply: Now, the Future
In 2022 tantalum demand was estimated to be 3,028 tons with a forecasted 6% annual growth rate through 2033.7 Tantalum ore supply is stronger than ever and ready to support the increasing demand from tantalum capacitor makers, semiconductor manufacturers, aerospace, additive manufacturing and other industries and applications. The past periods of supply instability, where real or perceived shortages caused disruption, should be behind all industry participants as more geographically diverse sources and novel mining methodologies are being introduced.
Tantalum supply as a co-product of lithium has grown dramatically. Just as the development of the internal combustion engine introduced the age of oil, the development of the lithium-ion battery for concentrated electricity storage for electric vehicles has now introduced the age of lithium.
Lithium and tantalum frequently co-exist in hard rock mines in Western Australia, South America, Africa, and elsewhere. This tantalum co-product is extracted with relatively minimal incremental environmental impact, predictable economics, and rising volumes. At mines where both minerals co-exist, tantalum and lithium are typically extracted from the same ore body and are transported and crushed together before the tantalum, which would otherwise be wasted, is separated for further upgrade.
Multiple industry analysts estimate a steep growth for lithium through 2040. Global lithium resources of all sources (brine and mineral concentrate) are estimated to be almost 400 million tons, compared to 273 million tons estimated in 2012.8 Tantalum as a co-product is found in some hard rock mines, particularly in Western Australia, with the two largest lithium and tantalum resources at the Greenbushes and Wodgina mines there. Current estimated global resources of tantalum co-product are over 37 million tons.9 The age of electric vehicles is bringing the age of lithium mining which provides additional tantalum sourcing. Long term lithium demand ultimately provides additional tantalum supply method and geographical diversity in addition to existing sources.
References
- Tantalum and Niobium-Based Capacitors, Yuri Freeman, Springer International Publishing AG 2018, Introduction xvi
- Capacitors World Markets, Technologies & Opportunities, Paumanok World Cap Report 2019, July 2019
- Websites of tantalum capacitor manufacturers
- Tantalum and Niobium-Based Capacitors, Yuri Freeman, Springer International Publishing AG 2018, page 32
- Roskill Tantalum Market Update, Analysis and Outlook, Roskill Information Services Ltd., London England, March 1995
- The Economics of Tantalum 10th Edition, 2009, Roskill Information Services Ltd., London England, September 2009, page 8
- Tantalum Review and Outlook, CPM Group, Brooklyn, NY, USA, June 2023
- Lithium Extractive Cost Model Service, Roskill Information Services Ltd., London England, June 2021
- Niobium and Tantalum: Chapter M of Critical Mineral Resources of the United States – Economic and Environmental Geology and Prospects for Future Supply, Klaus J. Schulz, Nadine M. Piatak, and John F. Papp, U.S. Geological Survey, Reston, Virginia, 2017