This article is based on ESA SPCD 2022 paper entitled “Low profile and solderless solutions for flat space interconnect” written by Nigel Kellett et. col, Axon’ Cable that was presented during the 4th ESA SPCD conference at ESA ESTEC, The Netherlands 11-14th October 2022. Published under ESA SPCD organisation committee permission.
INTRODUCTION
With one of the most diverse ranges of ESA QPL approvals and component specifications including wire and cable, multipin connectors, RF coaxial and High Data Rate cable assemblies, Axon’ Cable has a long heritage in the design and manufacture of robust and space-flight proven components and harnesses.
Since the early ‘90’s FFC (Flexible Flat Cable), also known within ESA as FCC (Flat Conductor Cable) has been a widely used technology outside space, predominantly within high volume automotive and consumer or office equipment applications. Now, however, with the increasing trend towards miniaturisation of satellites and the development of mega-constellations there is an ever-greater requirement for lower profile, lighter and solderless
interconnect solutions.
In this paper, Axon’ will explore a number of solutions currently in development:
- Development of Space-suitable Flexible Flat (Conductor) Cable
- Development of Space grade FFC/FCC/Flex connectors
- Development of Low-profile solderless PCB connections
SPACE-SUITABLE FLEXIBLE FLAT (CONDUCTOR) CABLE
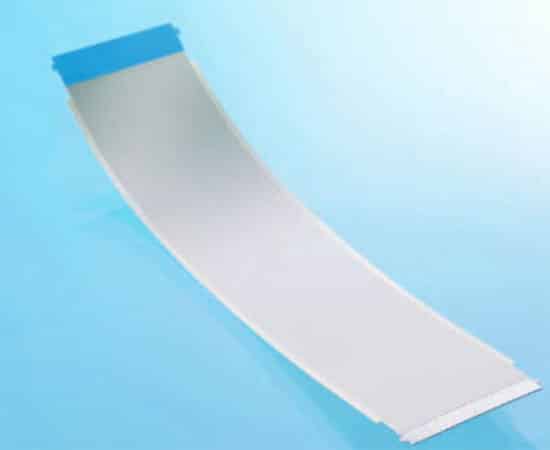
Conventional (non-space grade) FFC is typically manufactured as a ‘sandwich’ of copper or tin-plated copper flat conductors laminated between films of either PET or polyimide – with an adhesive layer. As shown in Fig. 1, the extremities of the cable are left uninsulated, and these conductors are then reinforced with a stiffener tape that creates a kind of plug out of the cable itself, suitable for insertion into industry standard Low Insertion Force (LIF) or Zero Insertion Force (ZIF) PCB connectors.
These cables are very suited to mass manufacture – Axon’ (for example) manufactures tens of millions of pieces per year – and depending on the variant they can be suitable for static board-to-board jumper applications, or for dynamic applications, such as a printer head or a steering wheel rotary connector, where millions of flexes may be required.
The materials used for these (terrestrial) FFC cables, however, are not directly suitable for space, particularly in terms of radiation, double insulation, outgassing and temperature. FFCs made using polyimide films associated with acrylic adhesive, however, have already been qualified for space in extreme conditions and development work is ongoing to develop varieties of FFC that could be used for a wide range of space flight applications. Moreover, FFC cables can be easily shielded using conductive tape. This is interesting from both EMC and signal integrity viewpoints.
To illustrate this an example of a AWG22 FFC designed for a power application is shown in Fig.2. Low and high-power connectors presented below in this paper have been designed to be compatible with this FFC. It is composed of 8 copper conductors (which will ultimately be silver plated) in a pitch of 5.08mm.
It is possible to assemble 2 or more FFCs such as the one in Figure 2 to create a shielded FFC pair as shown in Figure 3. For prototyping, tin plated copper shielding tape is used but this will be replaced by silver plated copper in the future. The tape is folded around the edges to provide 360° shielding and better handling.
A dedicated FFC has been developed for high-speed links. FFC is very interesting for this kind of application thanks to its highly regular geometry that delivers very low skew and to the flat conductor shape easing the high frequency signal transmission. Figure 4 shows a FFC with 4 impedance-matched pairs designed for SpaceWire transmission and which could also be used for other High Data Rate networks such as SpaceFibre or TT Ethernet. This cable uses 11 AWG28 conductors: 4 x differential stripline structure, (Fig.5) each pair being separated by a ground conductor for signal integrity.
Assemblies using FFC cables could be a very interesting alternative to round harnesses for signal, power and high speed harnesses. Axon’ is working with several customers to propose suitable cable and connector solutions for each of these segments. There is a real and growing interest in these technologies.
SPACE GRADE FFC/FCC/FLEX CONNECTORS
The space grade Flexible Flat Cable, or indeed Flex circuit, provides a clear opportunity to reduce space and weight in comparison to conventional round wire harnesses. However high reliability connection systems are needed for these cables and these are needed for in-line connections, panel-mount connections to equipment and direct PCB connections. Moreover, the flat shape of the FFC makes for significantly better heat dissipation than round wire bundles and can, therefore, also be very interesting for certain power links.
This paper provides a brief overview of the latest state of the art in space-grade connectorised FFC/FCC links, including the suitability of the link for different signal transmission styles, such as power, signal or high data rate.
Low power connection with FFC assemblies.
FFC links can be advantageously used for signal, low voltage and low current links for mass and volume savings. At the same time, the terrestrial LIF/ZIF style of PCB ‘sprung pressure’ connection, whilst considered acceptable for many consumer and industrial applications, may give rise to questions in terms of high reliability connections for space, particularly in terms of locking & electrical contact reliability, and double insulation rules.
Axon’ is working (Activity No. 1000031618 in the ESA-star system) to improve this otherwise well-proven concept by designing a ZIF connection adapted to space requirements. This solution has the space, weight, integration time & cost advantage of eliminating the connector mounted on the cable while keeping only the one mounted on the equipment. The elimination of a crimped or soldered joint also improves reliability.
Consideration also needs to be given to different constructions of FFC/FCC which lend themselves to different termination methods, such as soldering, welding or crimping. The first concept shown in Fig.6 is designed for AWG18 to AWG24. As mentioned above in this paper, it is based on a FFC of 8 conductors and a pitch of 5.08mm. The pitch allows us to be easily compliant with the double insulation requirement. (Either 2 different insulation layers required, or at least a 1.0 mm gap between adjacent conductor edges).
Conventional ZIF/LIF contacts are very thin to reduce the FFC pitch and maximise contact density. The Axon’ group is working on a new concept of ZIF contact using two lamellas folded on top of each other. A 3D model of this contact is illustrated in Fig.7. This is an interesting option for contact redundancy and contact resistance. The FFC conductor is placed between the two lamellas and then compressed when the ZIF connector is closed. The contact and conductor width makes it possible to pass more current than conventional ZIF connectors. Axon’ expects a rated current of 10A per contact.
Axon’ will also work on a more compact connector for lower AWG FFC and increase the contact density with, for example, a double row connector.
High power connection with FFC assemblies.
At the same time, Axon’ is working on the development of a power connector directly derived from the flight-proven Versatys® system (using #12 contacts) in order to realise power cabling based on flat cables. The flat structure of FFCs allows for very efficient radiated heat dissipation versus round wire constructions. Thus, for the same conductor cross-section, more current can be transported. With this higher current capability combined with the FFC’s low profile flexibility this could be a very interesting solution for solar array hinge interconnects, for example.
Just as with a ZIF connector, this power connector has been developed to be compatible with a FFC of 8 conductors and a pitch of 5.08mm. As compatible FFCs are AWG22 and AWG18, the contact size has been reduced from #12 of a standard Versatys® to #16. This connector is designed to be used with a shielded “packet” of 2 FFCs (as shown in Fig.8). The connection is consequently fully shielded thanks to the connector backshell. The angled shape of the backshell in this image is for a specific integration requirement, but straight backshells are equally possible. Axon’s D-Click fast-locking system is also used for rapid and tool-less integration.
High data rate assemblies using shielded FFC structure.
Axon’ has worked to replace in some cases LVDS, SpaceWire or TT Ethernet links traditionally made with round cable assemblies of 100 Ohms shielded pairs by a 360° shielded stripline FFC. Between each track an impedance of 100 Ohms is guaranteed and is very stable. By construction the intra- and inter-track skew are both very low (much lower than that of a conventional shielded twisted pair).
A 100 Ohm LVDS flat cable has been developed exhibiting similar or better performance than the classic ESCC round SpaceWire cables and an adaptation of the MicroMach® connector (developed with ESA specifically for 100 ohm high speed applications) for the flat cable shape has also been made. An assembly is shown Fig.9. These connections enable transmission rates in baseband up to 10 Gb/s over lengths of up to 75cm as shown in Fig.10. Furthermore, validation has been performed on a link connected to 2 PCB test jigs with a LAN tester overpassing TIA CAT6A ETHERNET channel limits mining more than 10Gb/s ETHERNET over lengths of up to 2m.
Thanks to its robust mechanical properties, this HDR FFC can also be completely folded over on itself several times along its length, which makes for a very convenient way of routing the link within the satellite or equipment.
LOW PROFILE SOLDERLESS PCB CONNECTIONS
There is more and more demand for solderless interconnect to PCBs, to remove the human element and manual intervention aspect of soldering, reduce our reliance on the tin and lead content, and to be able to make connections that can be easily disassembled if required. This paper explores one such solution, suitable for terminating flex-rigid circuits to a PCB, and which can then be terminated to a panel-mount MDM style connector, for example. Via a current project case-study, this paper shows how an ultra-low profile solderless device can be combined with fast-latching equipment MDM connectors to provide a high reliability solderless PCB connection, whilst at the same time ensuring high data rate LVDS performance, coupled with significantly better EMI performance than was previously possible.
Axon’ manufactures its own twist pin contacts used in standard Micro-D connectors. We took the opportunity to develop a customised twist pin compatible with an interposer system of connection. This technology exists in the market using lamellas or customized copper strands. The solution proposed by Axon’ has several advantages: it is based on the well-known twist pin and this delivers a high contact surface with the PCB pads. A concept illustration is given in Fig.11, the idea is to have the ‘bump’ of the twist pin protruding both above and below an insulative carrier tray. With a high contact area and a multiple contact points, the contact resistance is very low (less than 10mOhms under 2.5A).
This technology can be used in two configurations: High Data Rate (HDR) and low power connections. Regarding HDR connections, some tests have been carried out using our Axon’s MicroMach® FFC version soldered onto an impedance matched flex rigid circuit on one side and connected to a PCB using Axon’s interposer on the other side. A solderless PCB connection has been developed for this specific application as shown Fig.12.
Regarding low power connections, Axon’ developed a Micro-D shaped interposer to increase the contact density. The result is very similar to standard Micro-D space envelope. As shown in Fig.13, one of the applications is the connection of two PCBs to each other. As shown in Fig.14, another application is a harness composed by a Micro-D connector soldered to one side of a flex rigid circuit (could be a FFC cable in the future), the other side connected to PCB using the Axon’ interposer.
CONCLUSION
These developments are currently in the early stages. FFC assemblies have an undeniable interest for space applications given their electrical, thermal and mechanical properties, their potential for space and mass saving as well as being easy to integrate. However, an important work of standardization is necessary. Indeed, many FFC constructions exist, depending on conductor size (width, thickness), pitch, insulation materials, etc. An ESCC standard could help cable manufacturers and potential customers to integrate FFC assemblies in future space systems. All connector concepts presented in this paper will be further tested and characterised to evaluate their reliability under space environmental conditions and ultimately to confirm their usefulness for space applications.