Power electronic designers are continually trying to decrease overall design size by increasing conversion efficiency. One way they do that is by using Wide Bandgap (WBG) semiconductor devices. WBG devices can operate at higher switching frequencies and higher temperatures than traditional semiconductors. Their use allows reducing the size of passive components, bringing an overall more compact design and increasing power density per volume of the converters, thus making miniaturization mandatory. WBG devices also operate with extremely high voltage slew rates producing more high-frequency emissions.
Meeting the electromagnetic compliance (EMC) requirements of regulatory agencies becomes more and more complex for designs using WBG semiconductors, and electromagnetic interference (EMI) suppression capacitors play a crucial role. They must be miniaturized, to realize the benefits of smaller overall designs, but at the same time must meet high-reliability requirements under critical electrical and environmental conditions.
What Are EMI Suppression Capacitors?
EMI suppression capacitors are a specialized subset of commercially available capacitors that are designed for filtering electrical noise out of the power being supplied to the circuit. They do this by reducing the input impedance of the system for higher frequency noise.
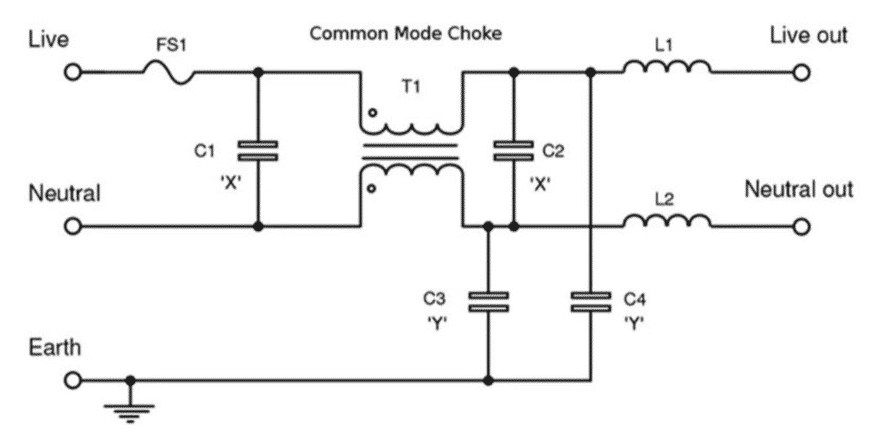
Source: https://passive-components.eu/addressing-design-challenges-in-emi-suppression-capacitors/
EMI suppression capacitors are often used to suppress noise on AC mains power lines. They are sometimes connected in ‘X’ configuration, or “between the lines”, as in C1 and C2 in the figure above. Other times, they are connected in the ‘Y’ configuration, or “line to ground”, as in C3 and C4. If a capacitor fails while in an ‘X’ configuration, there is a risk of fire. But if a capacitor fails while in a ‘Y’ configuration, there is instead a risk of electrical shock. Because of the danger of these failure modes, these capacitors are designed to fail “safe” to prevent fire or shock. For this reason, many EMI capacitors are also called safety capacitors.
How Are EMI Capacitors Rated?
EMI capacitors are classified by their intended use (X or Y configuration), their rated operating voltage, and the peak impulse voltage they can safely withstand. The subclasses and associated ratings for these capacitors are shown in the figures below.
Figure 2 and 3: Class-X and Class-Y Subclass Ratings Source: https://www.allaboutcircuits.com/technical-articles/safety-capacitor-class-x-and-class-y-capacitors/
What Are Harsh Environments?
Along with miniaturization, many designs need to operate in severe environmental conditions throughout their extended lifespan. Some examples include:
- On-board chargers for electric and hybrid vehicles, expected to withstand higher temperatures and extreme thermal shock cycles
- Miniaturized solar micro-inverters and smart energy meters with expected lifetimes of up to 25 years without servicing, in environments including potential high humidity factors
- Smart utility meters, expected to operate outdoors, reliably, for many years or even decades
To meet the needs of these harsh environment applications, a well-accepted accelerated life test standard for active and passive components has been developed in the electronics industry – the Temperature-Humidity-Bias (THB) test. The THB test has been recognized as an IEC standard for EMI suppression film capacitors. Capacitor manufacturers must indicate the THB grade for their certified solutions.
The tables below show the different Temperature-Humidity-Bias (THB) testing conditions per IEC Standards. The higher the grade, the more robust the capacitor is in harsh environments and longer extended life can be expected.
Polypropylene Film Capacitors’ Advantages
Polypropylene film capacitors (such as KEMET’s R53 series) typically offer wide capacitance range, AEC-Q200 automotive qualification in combination with long-life stability in harsh environmental conditions.
KEMET R53 series in addition offer compact size – its volume, on average, is 60% smaller than competitive X2 class capacitors, enabling a smaller PCB area, reduced weight, lower costs, and improved reliability.
Polypropylene film capacitors are well-suited for AC/DC converters in onboard chargers for xEVs, smart grid hardware, EMI filtering in Variable Frequency Drivers (VFDs), LED drivers, and high energy density applications such as capacitive power supplies.
The KEMET R53 X2 series polypropylene film EMI suppression capacitors exceed previous solutions and meet the IEC-60384-14 humidity robustness test with a Class IIIB classification. The R53 series achieves 1,000 hours during an accelerated life test under 85°C and 85% relative humidity at its rated AC (310 V) and DC (560 V) voltages.
Conclusion
Polypropylene film capacitors are among the best choice for EMI suppression applications in industrial and automotive applications thanks to its stability and long life at harsh conditions.
KEMET R53 series X2 capacitors can meet the highest THB class in a more miniaturized size than the competition. These key characteristics present significant advantages to designers in terms of both capability and space in the design. Additionally, the R53 AEC-Q200 qualification makes this series an ideal EMI suppression solution for automotive applications.