Polymer capacitors replaced electrolytic aluminum and manganese tantalum capacitors in many applications. While this trend was driven mainly by low equivalent series resistance (ESR) requirements in the past, high reliability performance is additionally requested for polymer capacitors nowadays. The development of new conductive polymers has opened the field of high reliability applications for polymer capacitors such as automotive, space and telecommunication. Even in consumer electronics, a trend to design in polymer capacitors having a higher reliability can be seen.
This paper presents the superior performance of new conductive polymer materials regarding harsh conditions such as elevated temperature and high humidity. State-of-the-art conductive polymers can not only achieve an intrinsically higher reliability but being much more environmentally friendly compared to previous polymer technologies.
The paper was presented by Udo Merker from Heraeus Epurio, Leverkusen, Germany at the 3rd PCNS 7-10th September 2021, Milano, Italy as paper No.1.5.
INTRODUCTION
For more than 25 years, applications of polymer aluminum and tantalum capacitors have been driven by low ESR requirements [1]. Traditional electrolytic capacitors were not able to meet these requirements of modern electronic circuits like motherboards. However, the application field of polymer capacitors was limited to consumer electronics mainly due to the lack of high voltage capability, relatively high DC leakage current (DCL) and low reliability performance.
During the last decade, these restrictions of polymer capacitors have been overcome and high voltage, low DCL and high reliability applications could be accessed. The rated voltage range of polymer capacitors has been extended from maximum of about 25 V to 400 V [2]. In combination with a superior DCL performance, the new polymer capacitors have been introduced in high reliability applications such as automotive and space [3,4].
MARKET TRENDS
While the COVID-19 pandemic has given an additional boost to the demand from consumer electronics in 2020/21, a strong and steady growth is emerging from automotive, communication infrastructure and industrial applications.
For capacitors used in such applications, the trend towards lower ESR, higher voltages and a higher capacitance density is ongoing and additionally a much higher reliability is needed. Life-time requirement can be as long as 10 years at a 100% duty cycle for telecommunication infrastructure. Temperature ratings of more than 150°C are requested in automotive. A high stability at harsh conditions like 85°C/85% relative humidity (RH) is necessary when for example air conditioning and cooling of data centers are omitted for energy saving reasons.
The development of conductive polymer dispersions for capacitor application paved the way for polymer capacitors to enter high reliability applications [5]. Further material improvement is necessary to cope with future reliability requirements.
CONDUCTIVE POLYMERS
Conductive polymers are applied as cathode material in electrolytic capacitors to achieve low ESR (Fig. 1). Traditional cathode materials like liquid electrolytes or manganese dioxide have orders of magnitude lower conductivity.
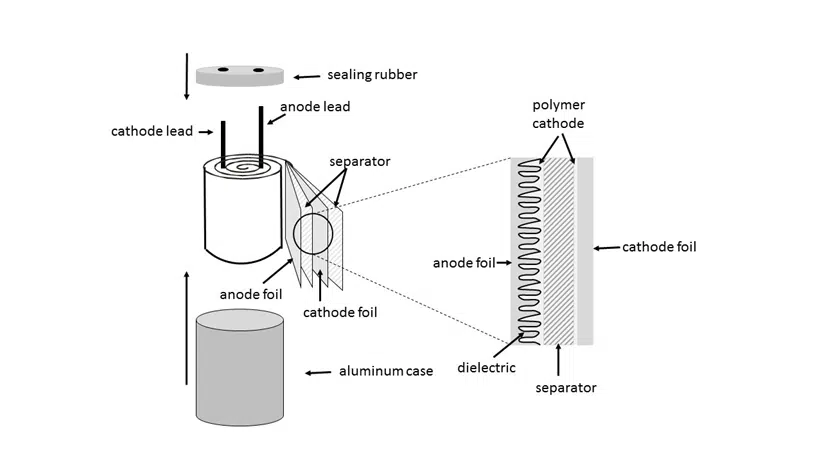
For aluminum and tantalum capacitors, a conductive polymer film is deposited by chemical in-situ polymerization of the monomer 3,4-ethylenedioxythiophene (EDOT) or from PEDOT:PSS conductive polymer dispersions on the dielectric which was formed by anodization of a porous aluminum or tantalum electrode (Fig. 2).
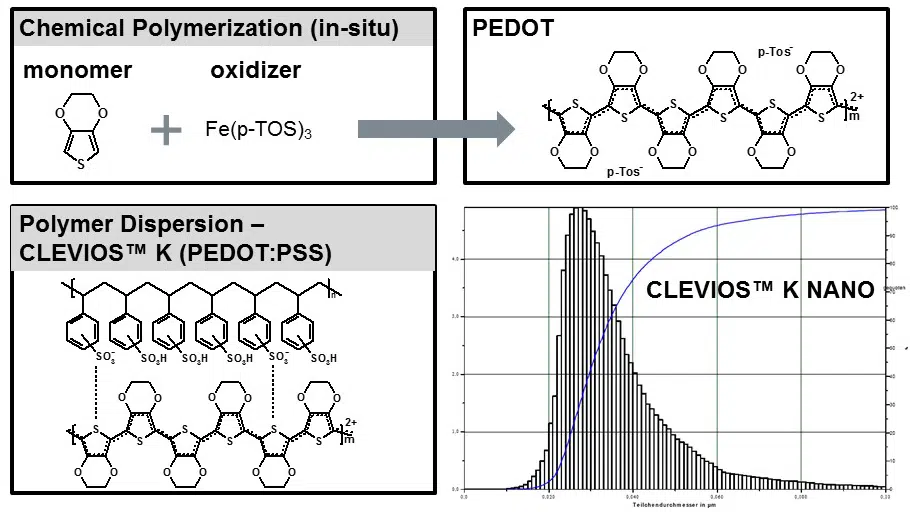
When conductive polymer dispersions are applied, the manufacturing process of polymer capacitors can be significantly simplified compared to in-situ polymerization by a dip and dry process without any chemical reactions. Furthermore, conductive polymer dispersions are water-borne and therefore environmentally friendly compared to organic solvent-based precursors for in-situ polymerization.
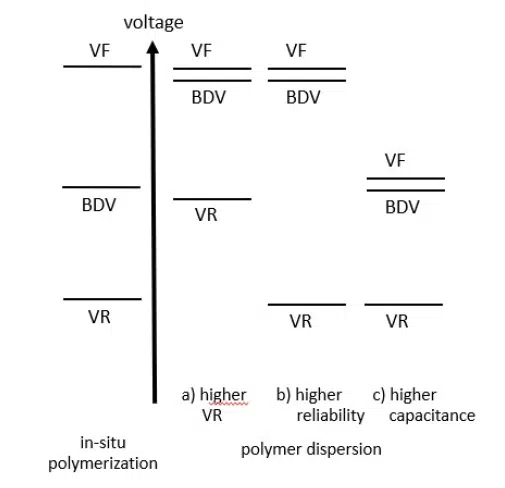
Besides process and environmental aspects, capacitors made with conductive polymer dispersions exhibit significant performance advantages over those for which an in-situ chemical process is applied.
The by far superior voltage performance is the most striking difference. With in-situ polymerization, voltage ratings only up to about 35V can be realized in an acceptable quality, while 400V is achieved with polymer dispersion [2]. The difference in performance is attributed to the particle nature of the polymer dispersions. In contrary to molecules used for in-situ polymerization, such particles cannot enter pinholes in the dielectric and do not deteriorate the break-down voltage (BDV) of the dielectric [6].
Since with conductive polymer dispersions the BDV is close to the formation (anodization) voltage (VF) of the dielectric and thus much higher than for in-situ polymerization, the rated voltage (VR) can be increased compared to in-situ polymerization (Fig. 3a). Or a much higher capacitance density can be achieved by reducing the thickness of the dielectric by applying a lower formation voltage (VF) (Fig. 3c). Alternatively, when keeping the formation (VF) and rated voltage (VR) at the same level as for in-situ polymerization, the difference between BDV and rated voltage (VR) is increased significantly by conductive polymer dispersions which results in a much higher reliability of the capacitor (Fig. 3b).
RELIABILITY
The conductive polymer as an organic material is the most sensitive part of the capacitor when exposed to high temperature or harsh conditions like 85°C/85%RH. The sheet resistance of films made from conductive polymer dispersions exhibit an extremely better stability at high temperature or 85°C/85%RH compared to in-situ polymerized films (Fig. 4). A temperature rating of up to 175°C for polymer capacitors seems feasible with such polymers in future.
We applied two approaches to further enhance the reliability of polymer capacitors: reducing the thermal load in the polymer layer and increasing the thermal stability of the polymer. A thermal load is induced within the conductive polymer by surge or ripple currents. A higher conductivity and a higher content of the PEDOT:PSS conductive polymer lower the resistance of the polymer cathode and thus limit the temperature rise when high electrical currents pass the capacitor. Additionally, we increased the density of the polymer cathode to dissipate the generated heat faster. The thermal stability was improved by reducing the oxidation potential of the polymer layer.
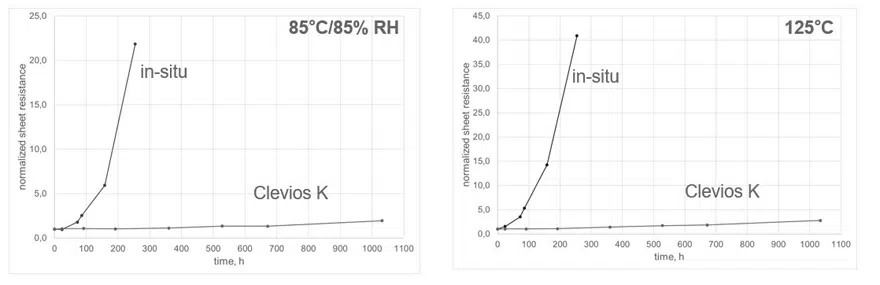
We have tested our newly developed Clevios K conductive polymer dispersion in aluminum radial capacitors. A lifetime over 1000h at 150°C without bias voltage could be achieved which is more than double the lifetime realized with a state-of-the-art polymer dispersion (Fig. 5). Actually, the lifetime was not limited by our new conductive polymer but rather the integrity of the rubber sealing after 1000 hours.
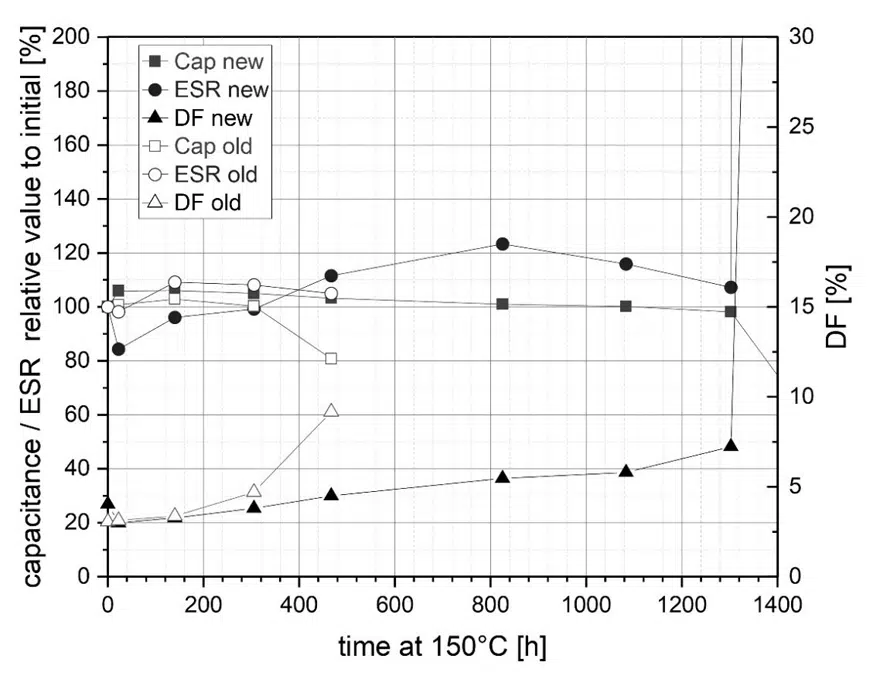
The aluminum capacitors made with our new polymer were stressed in a surge test by applying voltage cycles of 10s on/10s off with a peak current of 80A in each cycle. The capacitors withstood up to 2000 cycles while capacitors made with a state-of-the-art polymer dispersion showed significant capacitance loss already after 500 cycles (Fig. 6).
For some aluminum radial capacitor designs, a significant capacitance loss is observed at low temperature when conductive polymer dispersions are used. This limits the applications in automotive and industrial out-door applications. Our new product overcomes such limitation and exhibits a capacitance loss of less than 10% at -55°C (Fig. 7).
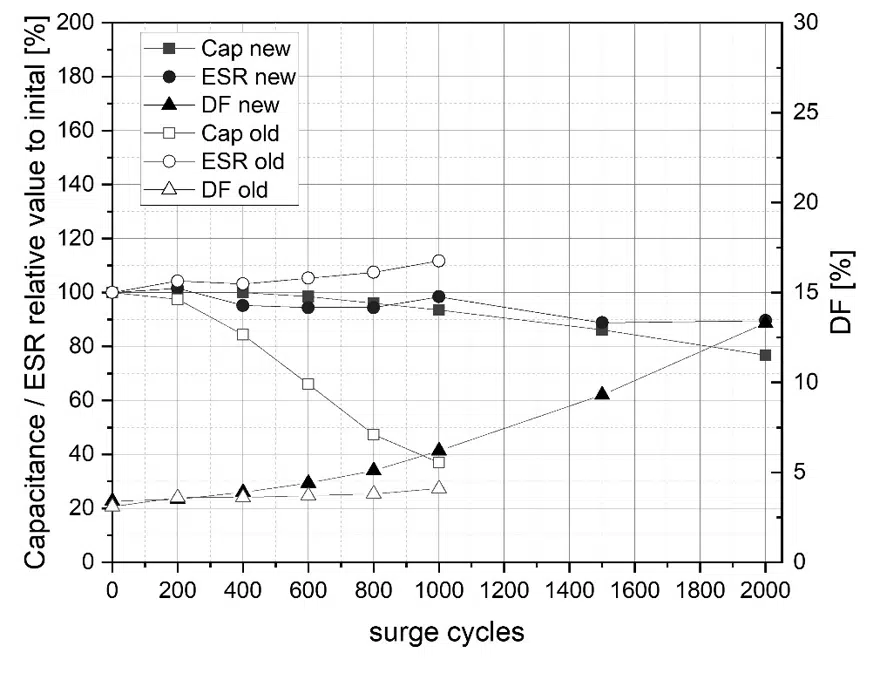
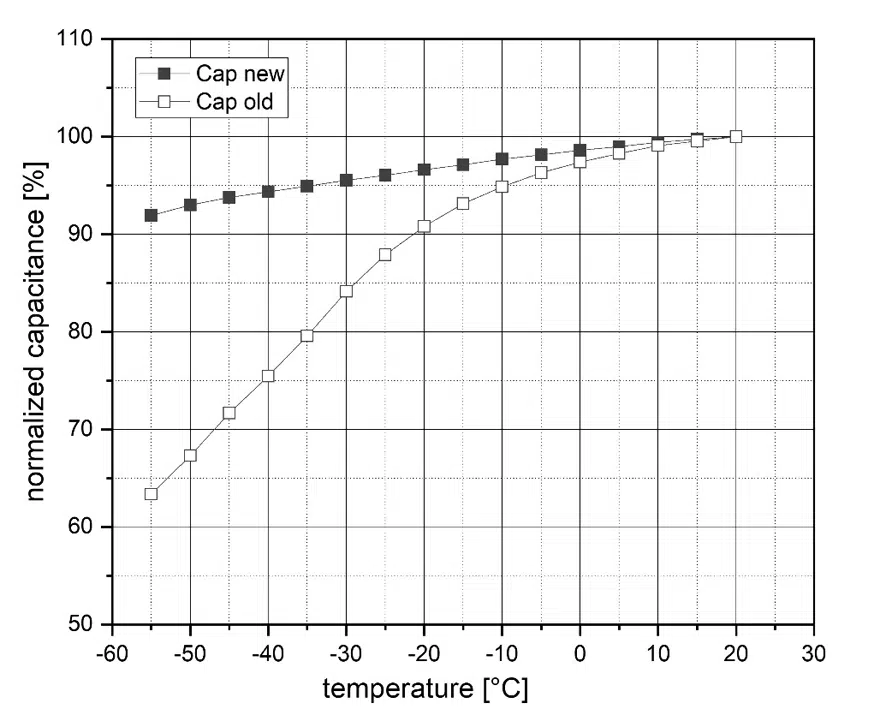
CONCLUSIONS
Conductive polymer dispersions have boosted the reliability performance of polymer capacitors significantly. Our next generation Clevios K conductive polymer dispersions further improves the high temperature stability as well as the surge and low temperature performance of polymer capacitors. This development supports the ongoing penetration of polymer capacitors into applications that require high reliability such as automotive, 5G telecommunication and industrial.
ACKNOWLEDGEMENT
The author like to thank Matthias Intelmann and Ralph Tillmann (Heraeus Epurio) for the preparation and measurement of the polymer capacitors.
REFERENCES
[1] A. Elschner, S. Kirchmeyer, W. Lövenich, U. Merker, and K. Reuter; PEDOT Principles and Applications of an Intrinsically Conductive Polymer, 2011, CRC Press, Boca Raton, USA.
[2] U. Merker et al; Next Generation of Polymer Capacitors: Boosting Performance of Electrolytic Capacitors with Conductive Polymer Dispersions, Proceedings of 1st Passive Components Networking Symposium, p. 75-79, 2017, Brno, Czech Republic.
[3] J. Petržílek, M. Uher, J. Navrátil, and M. Biler, Polymer Tantalum Capacitors for Advanced High Reliability Applications, 2nd SPACE PASSIVE COMPONENT DAYS 2016 – International Symposium, 12-14 October 2016 ESA/ESTEC, Noordwijk, The Netherlands.
[4] A. Tomás, C. Mota-Caetano, R. Monteiro, J. Vacas, and D. Lacombe, Ta SMD capacitors with MnO2 and Polymer Counter Electrode for Space Applications, 2nd SPACE PASSIVE COMPONENT DAYS 2016 – International Symposium, 12-14 October 2016 ESA/ESTEC, Noordwijk, The Netherlands.
[5] U. Merker, W. Lövenich, and K. Wussow, WO 2007/031207 (H. C. Starck GmbH), Priority: Sept 13, 2005.
[6] U. Merker, W. Lövenich, and K. Wussow, Conducting Polymer Dispersions for High-Capacitance Tantalum Capacitors, CARTS Europe, Sept 25-28, 2006, Bad Homburg, Germany.